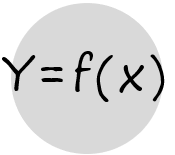
The products and services delivered by any organization are outcomes of processes. Any business activity whether it is industrial, commercial or service-oriented can be considered as a process. Effective management of these processes is key for organizational success. A process can be defined is a set of steps designed to produce a product or service, all with the aim of adding value to the customers. It starts with a business goal and ends with the achievement of the that goal.
When analyzing or designing processes, maximizing customer value should always be the top priority. This will help in achieving the competitive advantages in terms of quality, responsiveness and cost-efficiency. The outcomes of any business process should always provide increased value to the customer (thus enhancing effectiveness) while concurrently minimizing operational costs (thus improving efficiency). This requires the identification of important steps that add value from the customer’s perspective and the elimination of steps that do not add value.
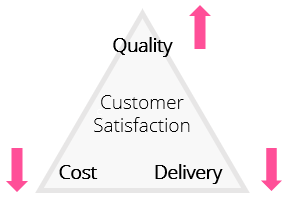
Many defects arise because something in the process is done incorrectly or inefficiently. To decrease defects and improve process capability and Sigma Level, we need to be able to address the problems that exist within the process. It is important to ensure our business processes are increasingly capable, and thus more predictable and profitable. Processes are incapable when the role of all factors and their influence within the business are not comprehensively understood.
Sigma Level is a capability index that is used to describe the performance of a process. A higher Sigma level indicates a higher process capability and that the process is less likely to create defects.
Almost everything we do at work or home can be broken down into a series of process steps. This makes it straightforward to identifying process inputs and outputs and understanding how they relate to each other. Another perspective on processes is that they are set of interrelated activities that together transform inputs into outputs. These activities are typically carried out by individuals, machinery, systems, automated processes, natural forces, or the combination of all.
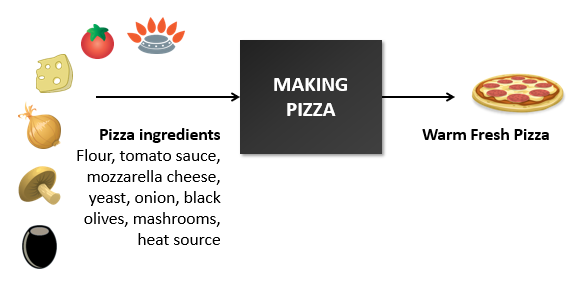
Any output (Y) is a function of a single or multiple inputs (X’s). To study and improve any existing process, it is important to identify and control the key X’s that affect Y. These key X’s are sometimes referred to as Key Process Input Variables. By knowing and controlling the factors that significantly impact process outcomes, processes become more capable, and hence, more predictable.
Key Process Input Variables (KPIV’s) are the input variables that have significant impact on the variability of the process.
Inputs are the variables, factors, causes, or sources of variation that may potentially lead to defects and waste. A key principle in Six Sigma methodology is the identification and analysis of these variables. Input variables can frequently be found within operation manuals, engineering specifications, or through discussions with operators and expert technicians A good first step involves walking through the process to observe and identify both input and output variables. Additionally, brainstorming sessions can be conducted to capture these variables comprehensively.
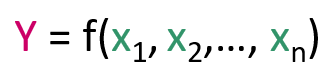
Processes can be categorized in many different ways. For example, they may be categorized as either automatic or manual, continuous or discontinuous, and core or supportive. One of the common ways is to categorize processes as either production or transactional processes. Production processes involve the flow of materials within a production environment and include activities such as machining, assembly, packaging. Transactional processes, on the other hand, involve the flow of information, humans, objects, tools and financial transactions within both production and service environments.


Further Information
What do we think of a process is not necessary what it actually is. Several techniques can be used for mapping and analyzing processes. These techniques will help exposing problems, finding performance gaps, and generating ideas for process improvement. Among these techniques, process maps stand out as one of the most straightforward and effective means of making sense of what happens or must happen in a process.
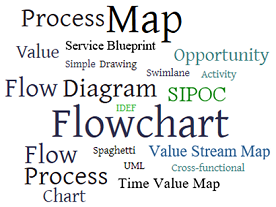
Wrapping Up
In short, an organization’s success relies on efficiently managing its processes to deliver products and services that add value to customers. Input variables are factors that influence process outcomes and need to be identified, understood and controlled. To find input variables, check manuals, specifications, talk to experts, or observe the process to capture these variables comprehensively.
Related Articles