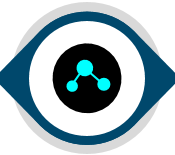
Also known as the Go See Technique, and Going to the Gemba.
Variants include Management by Walking Around (MBWA).
Many managers nowadays try to resolve work-related issues while they are sitting in their offices or conference rooms. Attempting to resolve problems in such way without visiting the actual place and without seeing what’s really happening is not necessarily a successful approach and may not always yield optimal results. This article will spotlight one of the most cost-effective data collection methods as well as one of the simplest and most powerful techniques of Lean methodology.
Observation is a data collection method used to gather specific information about a process or a situation. It allows the observer to collect the data in a real-time manner and from the location where the data is generated. Observation is intended to be a simple and straightforward learning method to better understand the actual ‘As-Is’ situation of daily operations. It is generally a cost-effectiveness method which requires nothing more than time and note-taking.
Observation has many important uses, including the collection of information about a process or situation, the verification of existing problems and issues, gaining an in-depth understanding of the current ‘As-Is’ situation, assessing actual performance in comparison to set targets, measuring customer satisfaction and quality perception, and acquiring best practices and benchmark data.
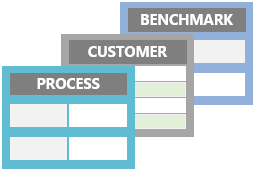
Observation is often used during process improvement and change management initiatives. It helps verifying existing issues and their potential root causes by collecting live data from the actual place where the work is being done. Additionally, it allows the observer to fully document the value stream of the process and measure the true performance. During these observation activities, specialized process observation forms can be used to record observed data, interview responses, improvement opportunities, and other valuable insights.
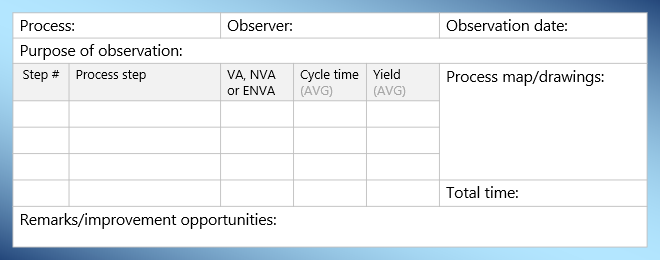
The applicability of observation extends into customer service environments. Oftentimes, there is a need to go to the customer’s site to truly understand their viewpoint and their interaction with the products and services. This approach is particularly useful for identifying customer satisfaction levels, providing valuable insights for ongoing improvement efforts. The key lies in carefully observing the interactions where the customer directly engages with the product or service.
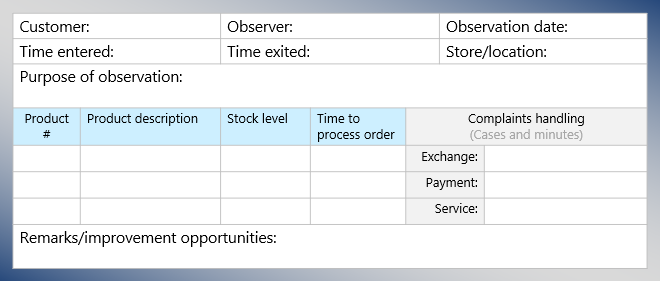
Types of Observation
- Silent observation: Useful when collecting raw data and typically takes only a couple of minutes to an hour.
- Interactive observation: Requires the observer to visit the actual place to observe the process, ask questions, and learn.
- Extended observation: The observation period takes much longer time to thoroughly understand the current state of a process.
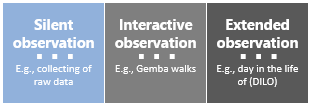
What is Gemba?
Gemba is a Japanese term that means “the actual place”. It refers to the real place where value is created and where clients are served within the value stream. In manufacturing environments, it often refers to the shop floor where products are manufactured and assembled. In the service sector, it refers to the actual place where services are delivered to customers, or where there is direct interaction between service providers and customers.
A Gemba walk is one of the most important Lean techniques to understand the current state of any given process. It is going to the actual place and observing how the work is performed. The purpose of Gemba walks is getting closer to the work and identifying potential areas for improvement. Keep in mind that these walks are not just some boxes that need to be checked, they represent, however, important steps in the ongoing journey of continuous improvement.
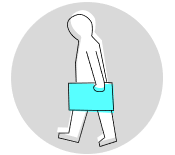
Regularly conducting Gemba walks is very useful in identifying various forms of waste and non-value-added activities, revealing opportunities for continuous improvement. These walks allow to gain valuable insights on variabilities, deviations from specifications, abnormalities, bottlenecks, redundancies, unsafe acts and conditions, and 5S improvement opportunities. Furthermore, Gemba walks allow the observation of positive behaviors and good practices, for example, someone who is picking up garbage while walking and throwing it in the trash.

Be careful not to confuse Gemba walks with auditing. Auditing focuses on ensuring compliance, while Gemba walks are concerned with uncovering problems that impact performance.
Gemba walkers should focus their attention on the flow of items through a process, such as products, tools, applications, materials, and information. They can also focus on the flow of human activities, especially in the service sector like transportation and hospitality. The ultimate goal is to find out what is really happening and not what is supposed to happen or whether people are following procedures or meeting deadlines.
Gemba walks involve interviewing people, taking their feedback, evaluating their needs, and implementing plans and solutions that will effectively solve their problems and streamline their work. People should view these walks as to support them with their needs and issues. When talking to people, be empathetic and supportive, and listen attentively to their concerns and suggestions. It is also important to avoid providing solutions or judgment, and instead, behave more like someone who wants to learn and support.

While Gemba walks share similarities with Management by Walking Around (MBWA), the latter places greater emphasis on strengthening the relationships with people and creating an environment of trust in the workplace.
Conducting an Observation
There is no really defined approach to conduct an observation, however, the following points can serve as a useful guide:
- Clearly define the purpose of the observation and how the observed information will be used afterward.
- Study the process or problem you are about to observe.
- Prepare an observation form for collecting the desired information.
- Get permission from the process owner or supervisor to conduct the observation and talk to the people there.
- Conduct the observation. Visit the actual place where the process or problem takes place.
- Walk the process, collect data, interview people, and record observations and responses.
- Take time to document important ideas and findings soon after completing the observation.
- Share what you have learned in your operational meetings.
- Take the necessary steps to resolve the problem and improve the process.
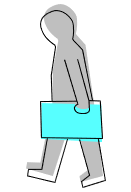

There are many online templates that can be used to conduct and manage your Gemba walks. One of the simplest and most straightforward ways is to use this Gemba walk template.
Wrapping Up
Observation is a powerful tool that involves physically being where the work is done to understand the current situation, verify problems, document processes, assess performance, and gather insights. Specialized observation forms can enhance this process by recording data and insights. Gemba walks involve the practice of visiting the actual work site to directly observe processes, engage with employees, and collect real-time data in order to gain insights and identify opportunities for process improvement.
Other Formats
Do you want to use the slides in your training courses?

Observation Training Material – $18.85
Related Articles
Related Templates