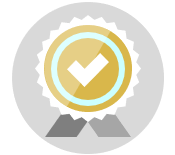
Also known as standardized work and Standardization.
Variants include Interchangeability.
Standard work means working on standards to produce correct and consistent results. It is considered a way to achieve the highest possible degree of consistency and reliability in any process. It aims to ensure that all activities are done by everyone in the same way and in the best possible way. Standard work is one of the important elements of Lean thinking and is essential for Lean to be successful. Lean organizations rely on standard work in order to create a baseline from which they can improve.
Standard work is key to continually improving business processes and an important part of any sustainable change effort. Standardized processes provide more consistent results as the chances for variation will be reduced since the activities are always executed in a consistent manner. It is important to acknowledge that a problem is a deviation from a standard or expectation. Therefore, standard work is about identifying problems and making waste and inefficiencies visible in order to drive continuous improvement.
Additionally, standard work provides a way of maintaining improvements achieved during improvement activities. Oftentimes, we face a situation where a previously concluded project needs to be opened again. This indicates that the problem was not effectively dealt with or the absence of measures to sustain the gains achieved. Thus, successful solutions must be standardized in order to maintain their effectiveness over the long term.
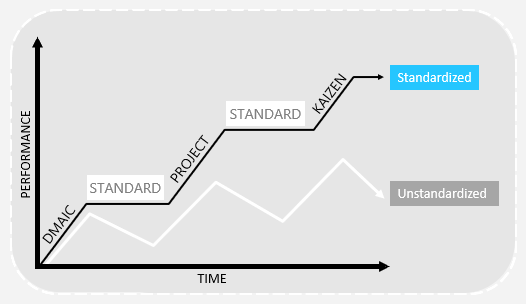
Standard work is an approach that is based around human actions and motion. It considers the actions performed by humans, systems or the combination of both to create value-added contributions. The aim is to create the most effective sequence of activities while minimizing delays and other forms of wastage to increase efficiency and productivity. Therefore, it is important to identify the right process steps, their sequential arrangement, and the allocation of appropriate timeframes prior to standard work implementation.
Standard work documentation may contain written instructions, photos, drawings, illustrations, charts, or any other suitable method necessary to clearly communicate the standards. Visual representation of standard work promotes visual management and is considered a great way to clarify and communicate the standards to everyone. It facilitates demonstrating difficult concepts and improves the detection of abnormalities and errors. Process steps can be illustrated with photos and graphs which will attract people to read and engage.
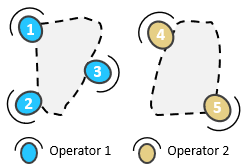
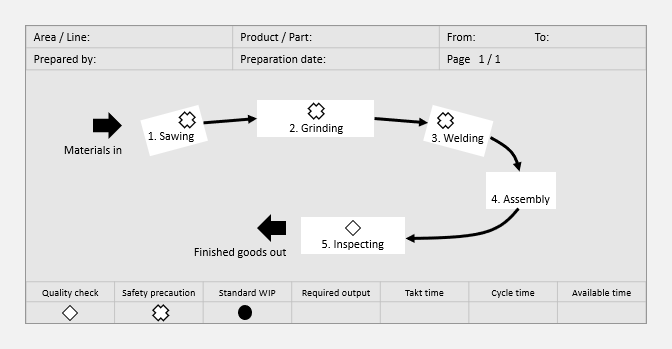
Standard work is also an invaluable training tool, serving as the basis for training both existing and incoming staff in their respective roles. For this reason, it should be documented at the lowest possible level, ensuring it fully covers all the details of how activities are done. Additionally, standard work can be useful for preserving the know-how of the optimal work practices. It also provides point of comparison so we can compare what is happening with what should be happening. That’s why they are considered important resources for auditing, assessment, and performance evaluation.
Ideally, standard work documentation should be created by those who are directly engaged in the execution of the work. People are more likely to accept and adhere to the standards if they help in crafting it. While other stakeholders, such as subject matter experts and engineers, may provide valuable insights, the active participation of the process workforce remains crucial. Moreover, the documentation of standard work should be readily accessible at the point of execution, ensuring visibility and ease of access for all personnel involved in the process.
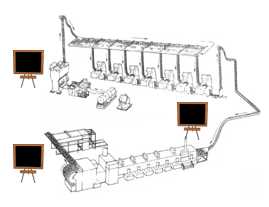
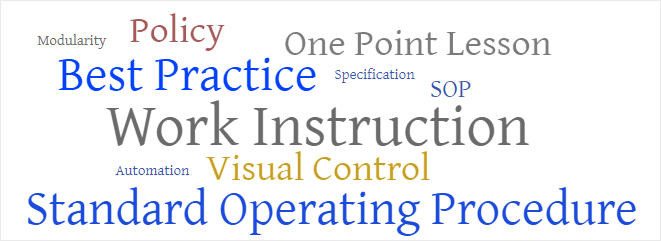
Standard Operating Procedure (SOP)
Standard work can be embedded within a company’s operations through the utilization of Standard Operating Procedures (SOPs). An SOP is a document that describes the best way to execute a process to maintain consistent work and achieve optimal results. It aims to standardize the way work is performed and make it easier for everyone to do their work. Developing and implementing SOPs enable standard work to be effective and help communicating these standards to personnel engaged in the operation.

SOPs are often used in improvement projects for documenting standardized and improved processes. Successful solutions must be standardized in order to remain effective over the long term. SOPs can also be used to document key and critical processes, complex processes, and highly repetitive processes. However, a typical challenge encountered in the development of SOPs is to have a balance between providing sufficient detail and avoiding unnecessary complexity.
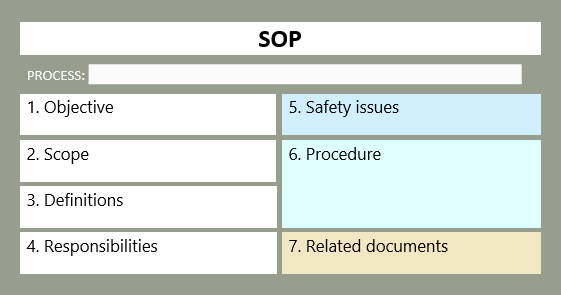
Developing an SOP
The following guidelines can serve as a roadmap for the development of SOPs for newly improved processes.
- With your team, clearly describe the purpose for developing the SOP.
- Understand the existing system for standard work and the current SOP if exists.
- Identify the key process activities and collect any required information.
- Prepare a draft of the SOP by describing the process activities, their sequence and time frames.
- Share the SOP draft with the concerned stakeholders including the employees working on the process. Ask them to review and suggest ideas that will further improve the SOP.
- Test the SOP by having someone performing each step exactly as it is described.
- Make the final draft of the SOP and distribute it to all relevant parties.
Example – Manufacturing
Presented below is an illustrative SOP example created for the label changeover process within a manufacturing facility.
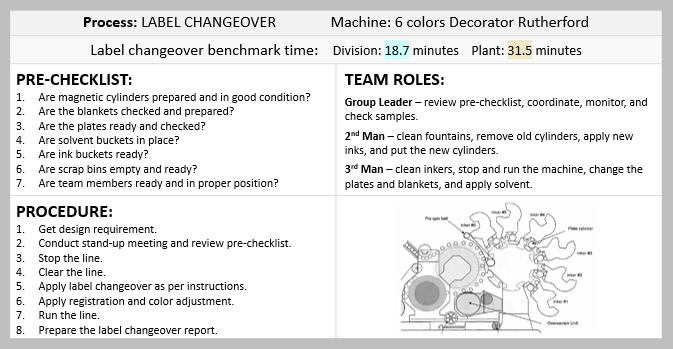
Example – Service Environments
The following is another SOP example which was created for the order process in a service-oriented environment.
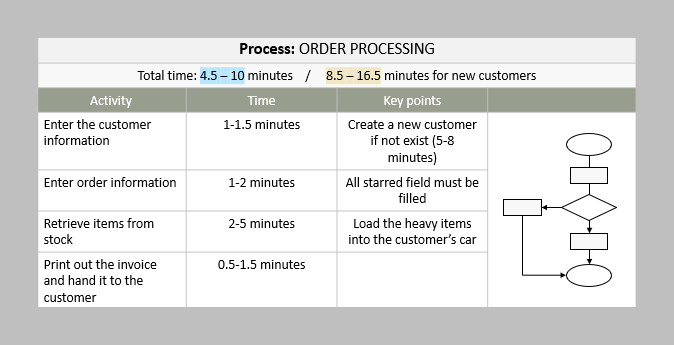

There are many tools that can help you documenting your SOPs. One of the most straightforward approaches involves the utilization of this SOP template.
Wrapping Up
In conclusion, standard work plays an important role in achieving operational consistency and reliability. This approach drives continuous improvement and serves as a framework for maintaining long-term effectiveness. Standard Operating Procedures (SOPs) are tools to implement and maintain standard work. Finally, documentation, such as SOPs, visual aids, and detailed instructions, communicates standards effectively and helps embed these practices into daily operations.
Other Formats
Do you want to use the slides in your training courses?

Standard Work Training Material – $18.85
Related Articles
Related Templates