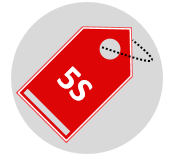
Also known as Five S and Workplace Organization.
Variants include 6S.
The 5S methodology is an improvement tool for organizing and maintaining a disciplined and productive workplace. It facilitates the creation of a better working environment by reducing waste while improving efficiency, safety and quality. 5S represents five fundamental practices that starts with the letter ‘S’. It is commonly applied by manufacturing facilities in production lines, storage areas, maintenance areas, and offices. It is now being increasingly applied across diverse industries including health care, logistics, hospitality and construction.
Rooted in Japanese management principles, 5S was originally developed by Toyota as an integral component of their Lean production system. It is considered an important component of Lean Thinking and a prerequisite for driving other Lean techniques such as TPM and flow optimization. Many companies start their Lean transformation journey with 5S because it is one of the easiest Lean techniques and exposes some of the most visible examples of waste. Many experts believe that you need to be successful with 5S so you don’t struggle with the other techniques during Lean implementation.
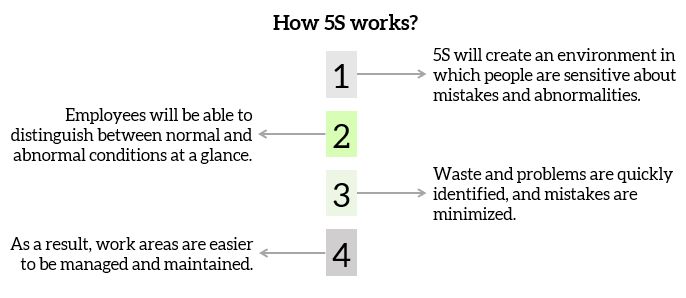

One main issue faced when implementing 5S is that cost savings typically cannot be captured in most costing systems. There will be soft-savings in terms of quality, safety and employee morale, however, there will be no hard-savings that can be measured and tracked. One way to justify the value of 5S is by measuring the reduction in waste as a result of performing 5S activities.
The 5S Phases
The term 5S is an abbreviation for five Japanese words: seiri, seiton, seisou, seiketsu, and shitsuke. These five words are often translated into English as: sorting, setting in order, shining, standardizing, and sustaining. Other English translations are also possible.
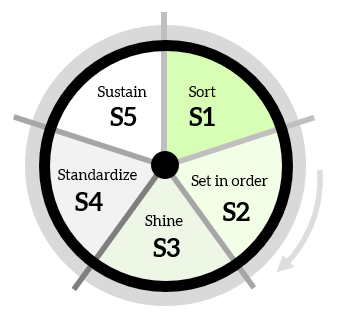
Sorting
This phase refers to the practice of going through all the items within the workplace and keeping only what is actually needed. Items which are excess to requirements should either be stored offsite, sold, scraped, or discarded. The main idea behind this phase is to clear the area from distractions to concentrate on what remains in the workplace. This leads to less clutter and wasted time, frees up valuable space, and creates a more streamlined workplace.
Some of the strategies used in Sorting are:
- Inspect all items in the workplace then define what is necessary to perform the work. Keep only what is needed and remove everything else.
- Remove items which are unusable, broken, outdated, redundant and occasionally used.
- Do not allow secret warehousing of parts or tools.
- Remember to sort out unnecessary documents in files.
- Don’t forget computer files and emails. Archive or delete files that are no longer needed.
- Define standards for eliminating unnecessary items and for waste disposal.

A widely employed tool during the sorting phase is the Red Tag technique. It is a labeling tool used to highlight what is necessary within a specific area. The objective is to determine if anyone thinks an item is necessary and in what quantity. Items are red tagged for a limited period of time during which their usage is evaluated. After one week or two, items that remain unused or unneeded after this period should be either relocated or disposed of, resulting in a less distracting workplace.
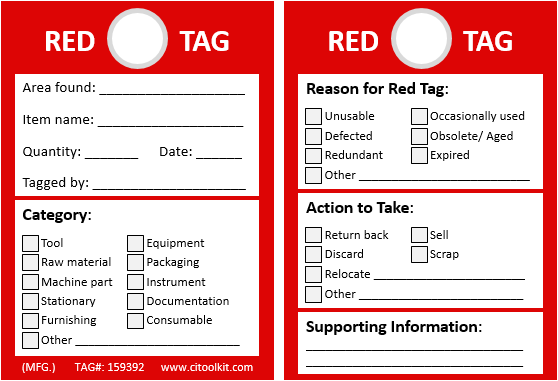
Setting In Order
Setting in order refers to the practice of arranging the required items to optimize accessibility. It defines where and how items to perform the work should be located and organized. Once you have eliminated all the unneeded items, get back to the left items and organize them in a way that makes it easy to find what is needed. It should be obvious at a glance if things are not where they are supposed to be. This approach reduces wasted time and motion, improves process workflow, and contributes to overall efficiency.
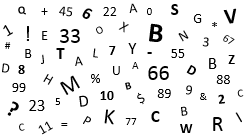
Some of the strategies used in this phase are:
- Assign positions for all equipment, tools, parts and materials.
- Store items by frequency of use and at the point of use.
- Organize normal items in modular cabinets, drawers, shelves and racks.
- Organize small items into storage bins, boxes and cans.
- Organize large items in standard well-labeled floor or outside areas.
- Change to an open storage system. Eliminate locks and covers as they hide secret inventory and lost parts and tools.
- Improve wiring organization.
- Place shared tools on shadow boards.
- Use different colored paint or tape to assign tools for different departments or individuals.
- Use functional carts when conducting changeovers, maintenance or cleaning.
- Ensure safety equipment is easily accessible.
- Keep clear standardized labels on work areas, doors, shelves, boxes, bins and hangars.
- Use tape or paint to mark and label floors, isles, storage areas, parking areas, delivery areas, staking areas, and the locations of safety equipment.
- Stack pallets correctly and ensure FIFO is being followed.
- Use colors and labels to define inventory levels and reorder triggers.
- Use a tool checklist to ensure all the proper tools are available.
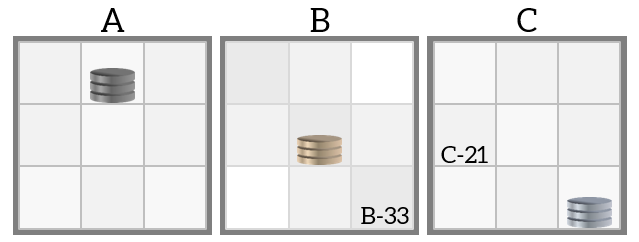
Shining
The shining phase is all about keeping the workspace very clean without rubbish, dirt or dust. This enables the easy identification of abnormalities such as repeated contamination and oil spills, preventing them from getting worse. Moreover, maintaining a clean and orderly workspace helps in creating a sense of ownership among employees, making it safer and more pleasant to work in.
Some of the strategies used in shining are:
- Eliminate all forms of dirt, contamination and clutter.
- Thoroughly clean, dust, polish, wash and sweep on a regular basis.
- Clean all tools, machines, and equipment.
- Clean even the places where most people do not notice.
- Clean up spills on floor and walls and ensure they are in good condition.
- Make sure floors and isles are empty as possible.
- Divide the workplace into zones and allocate people to take charge of each zone.
- Establish a duty schedule and assign responsibilities.
- Identify the waste disposal storage area and regularly clean it.
- Ensure cleaning tools and materials are easily accessible.
- Use cleaning inspection checklists.
- Paint floors, walls, machines and tools.
- Don’t forget computers, furnishings, cabinets, storage bins, workstations and display boards.
- Use fault identification tags while cleaning to indicate any faults.
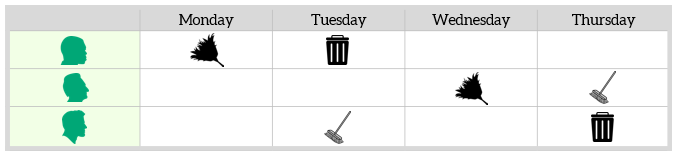
Standardizing
Keeping the workplace clean and tidy is a real challenge and can only be achieved if standards are established and adhered to. The standardize phase involves implementing clear guidelines for maintaining cleanliness and orderliness. Over time, these standards should be updated to streamline 5S practices, ensuring continued simplicity and ease of implementation.
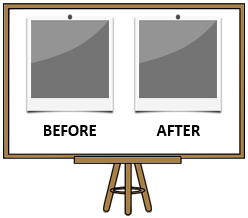
Some of the strategies used in standardizing are:
- Establish procedures and schedules to ensure the consistency of implementing the first three ‘S’ practices.
- Ensure everything is done by everyone in a similar manner.
- Use photos and short instructions to help keep everything as it should be and remind people of the standards.
- Post standard guidelines, area maps and ‘after’ photos in visible places.
- Use easily understandable words and phrases.
- Establish basic standards to be followed including color coding, signs and labels design.
- Introduce visual management practices to promote consistency and create process stability.
- Review the status of the work area regularly using 5S audit checklists.
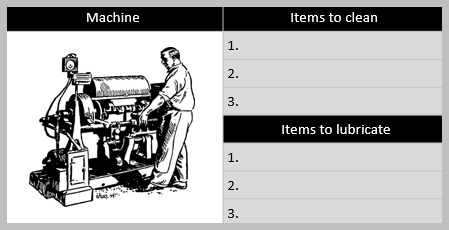
Sustaining
Once the first four phases have been implemented, attention must shift to sustaining what has been accomplished. Sustaining is the disciplined application of the first four ‘S’ practices to ensure the effectiveness and longevity of the 5S program. This phase proves to be one of the most challenging parts of implementation, as many companies have found themselves with cluttered and dirty workplaces again after their initial attempt to implement 5S.
5S has a tendency to fail when there is a lack of ownership from the top and when leadership does not place continuous focus on it. Leadership must buy-in and be personally committed to ensure the success of the 5S program. They must establish a culture where 5S excellence is expected and nothing less is tolerated. Adequate planning, training, monitoring, and a formal system of accountability must exist in order for the 5S program to ensure its successful continuation.
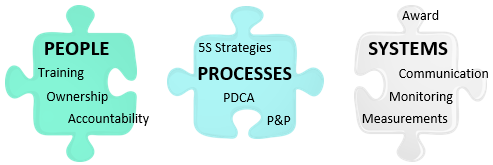
Some of the strategies implemented to sustain the gains include:
- Ensure everyone in the company knows the benefit of implementing the 5S program.
- Ensure everybody is participating and held accountable.
- Train everyone on the 5S principles.
- Make 5S part of the new employee induction process.
- Ensure all areas are covered by the 5S program.
- Improve the work structure to support the new practices.
- Enforce the standards through policies and procedures.
- Make it part of health and safety.
- Make it part of daily Gemba meetings and Kaizen events.
- Use 5S posters and signs to remind of the benefits.
- Audit the effectiveness of the 5S program.
- Monitor results through appropriate metrics and analysis.
- Communicate audit and performance results to all employees.
- Reward and recognize the efforts and accomplishments.
Implementing 5S in One Area
One of the best approaches to implement the 5S program is to start with a pilot area and use it as a model for the rest of the work areas. This gradual implementation will increase the likelihood for a successful transition later on. Start with whatever simple or find a problem for which 5S will play a key role in its resolution. Keeping it small and simple is better than starting big and having too many issues to handle at once.
The following steps describe how to implement 5S in one area:
- Establish a 5S team and appoint a team leader.
- Ensure the team understands the goals of implementing the 5S program.
- Observe the area and evaluate the current situation.
- Collect data and take the ‘BEFORE’ photos.
- Brainstorm with the team to identify opportunities for improvement.
- Establish an improvement plan that details the activities, responsibilities and timeframe.
- Implement the plan and spend proper time on each ‘S’ to implement the strategies.
- Audit the area and take the ‘AFTER’ photos to showcase the improvements.
- Develop and implement a control plan to sustain the improvement in that pilot area.
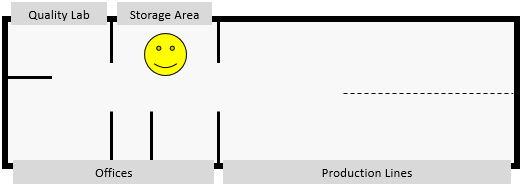
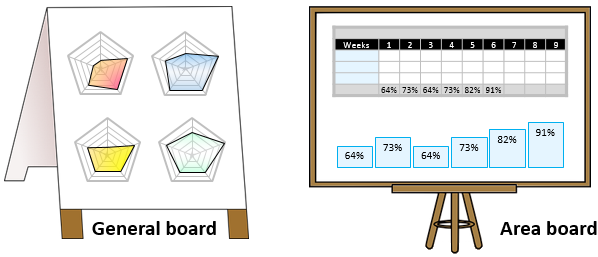

The progress and effectiveness of the program should be evaluated regularly. This can be achieved using a 5S Audit Checklist which should end up with a list of improvement actions.
Wrapping Up
5S is a structured approach to establishing and sustaining an organized, hygienic, safe, efficient, and productive workplace. It is not just about the appearance and keeping the workplace tidy, nor it is a housekeeping technique; rather, it is more a way of eliminating waste, creating a smooth workflow, and identifying opportunities for improvement.
With 5S, excessive inventory and parts, wasted motion, and time spent searching for essential items can be substantially eliminated or reduced. This will not only make everybody’s jobs easier but also boosts employee morale and creates a feeling of ownership and motivation.
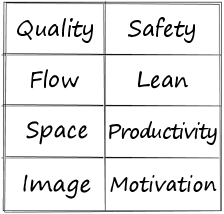
Other Formats
Do you want to use the slides in your training courses?

5S Training Material – $26.85
Related Articles
Related Templates